Work Portfolio
Zimmer Station 2016 - Current
In Progress
Apache Station 2011 - 2016
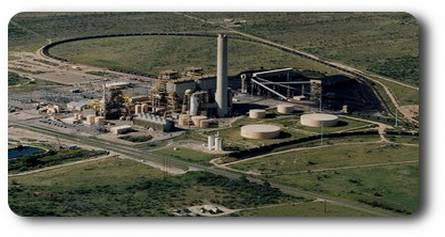
Apache Station is a rural electric cooperative plant that serves portions of Arizona and California. Constructed over time as demand grew, the units at Apache now include:
- Two 195MW steam units that can burn coal or natural gas
- Coal blending facilities
- Hot side electrostatic precipitators
- Wet FGD scrubbers
- A 75MW natural gas boiler that operates in combined cycle with a gas turbine
- Four gas turbines that have outputs ranging from 10MW to 65MW
Altogether, the plant's peak output is 605 megawatts. Due to the types of equipment and the time range of the construction, Apache Station has a diverse set of control systems and requires an understanding of many different systems and physical phenomena to address all the unique engineering issues.
LM6000 Controls Retrofit
General Electric notified the plant that the end of support was approaching for the Mark VI Millennium controls in the plant's LM6000 aero-derivitive turbine. I was asked to oversee a project to replace the controls. Five vendors were selected and closely examined. Using a Kepner-Tregoe project analysis method, I lead a multidisciplinary through a review of each vendor and their attributes.
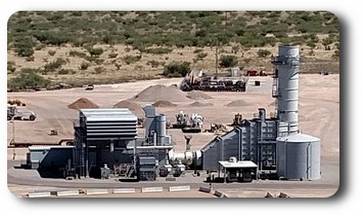
After the project was awarded, I continued as the project manager for the controls replacement. This included outage planning and scheduling, factory acceptance testing, in-house HMI and database modifications, demolition, installation, commissioning, and training. Prior to the upgrade, a list of existing deficiencies was created and then corrected as part of the upgrade. The turbine is now much more reliable than before.
This project also incorporated the first virtual SCADA and HMI systems at the plant. The benefits of virtualization expedited the development of the HMI system.
Ovation Controls
The Emerson Ovation distributed control system is used for turbine, boiler, and burner control at Apache. I was the person responsible for maintaining the servers, controls, IO, and logic.
During my time at Apache, I upgraded three control systems from 3.3.1 to 3.5.1, replacing the older controllers with the newest version, OCR1100 controllers.
I was frequently called upon to troubleshoot process issues with with Ovation's live logic diagrams and historical trending software.
I authored many logic additions and changes. These changes include modifying boiler feed water flow controls, O2 probe signal conditioning, incorporation of triple redundant drum level and pressure transmitters, many 4-20 control loops for position and pressure, and boiler tuning for O2. I have also tuned the principal process control loops for stability and adjusted them for unusual conditions.
LVDT Upgrades
The original 5 wire LVDT's in service on a main turbine were obsolete and created an extended downtime risk. Altogether, there were seven location where LVDT's either needed to be installed. After receiving a very high quote from a vendor, I elected to do this project in-house.
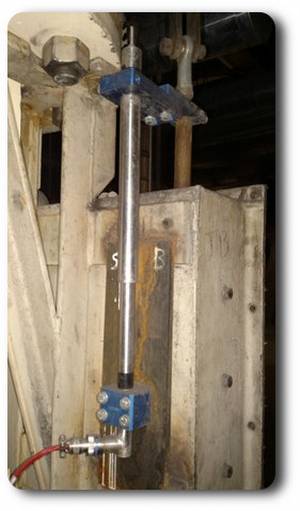
As the plant controls engineer, I determined the LVDT specifications and necessary cables, worked with our machinist to design and fabricate the required mounts, oversaw the installation during a plant outage, reconfigured the controls to work with the new LVDT's, and commissioned them during start up. I also routinely calibrated the LVDT's as required.
Water Tower Level Controls
Several of the capacitive type level probes in the plant water tower at Apache had failed. With the assistance of the plant electricians, I addressed this by installing a Rosemount guided wave radar level transmitter at the top of the water tower.
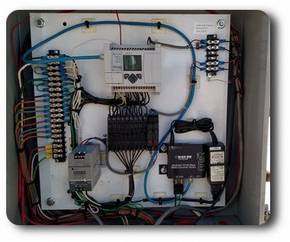
It was cost prohibitive to run a new analog signal cable from the level transmitter to the controls for the raw water pumps. Instead, the analog level signal is now monitored by a small PLC at the base of the tower. The PLC then emulates the on-off states of the previous level probes using the original control cables for pump control. The PLC also allows the level at which pumps start and stop to be adjusted.
Finally, the PLC was connected to the control network at a nearby switch, allowing the analog tower level to be monitored by the operators on a new HMI graphic.
Feed Water Bypass Valve Actuator Replacements
The two coal units at Apache each have three valves to control water flow to the boiler, a start-up regulator, the main regulator and an electrically operated bypass valve. The positioning electronics in each of the original bypass valves had ceased working, making them unusable for service. To remedy this, we replaced the failed actuators. My role in this project was to see that the actuators were correctly integrated into the DCS IO, and to commission the new actuators. Additionally, I created new logic that allows the start-up regulator and the bypass valve to work in tandem. Because they are electrical and not pneumatic like the start-up and main regulator, the bypass valves can not modulate continuously. By using the start-up regulator to trim the feed water flow, the bypass valve is allowed to rest most of the time this control mode is in use.
Centac Compressors
Apache utilizes two Centac air compressors to provide plant, instrument, service, and soot-blowing air. I managed multiple recent rebuilds for both. In addition I replaced the aged Bentley vibration monitoring system with a state-of-the-art Allen-Bradley vibration monitoring system.
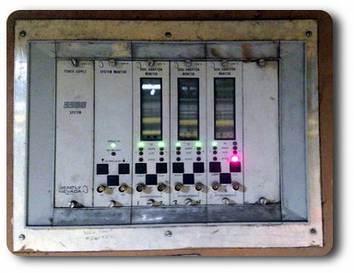
Finally, I created logic and performed tuning changes in the compressors' controls to prevent compressor surging when the machines transition between pressure set points. The time between rebuilds has gone from an average of 2.5 years to over 5 years.
Gas Scrubber Controls Upgrade
Each coal unit has a sulfur dioxide absorption system (SDAS).
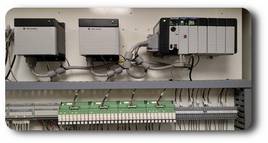
All the controls for the dampers, pumps and valves were constructed of hard-wired relay logic, which was deteriorating and becoming unreliable. Additionally, this relay system had been modified and not all the modifications were documented. Rather than trying to re-engineer and repair this, management decided to allow me to develop a PLC based control system in-house, including all the pumps, valves, level controls and pH controls as well.
As the project manager and controls engineer for this project, I developed the IO lists, specified the hardware, created installation prints and tables, oversaw the installation by the plant electricians and instrument technicians, and recommissioned the system. The SDAS now operates more reliably and has a modern HMI interface which can be operated from the control center instead of the local control board pistol grip switches.
High Pressure Feed Water Heaters Level Controls Upgrade
Each steam unit has multiple high pressure feed water heaters. These feed water heaters were controlled by the original pneumatic PID level controllers. The controllers had fallen into disrepair, and the technicians who were knowledgeable in how to service them had retired. Heater levels were swinging from HIHI to LOLO several times each hour. This situation increased the risk of a water induction event and exhausted the operators with the constant alarms.
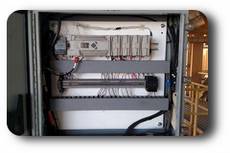
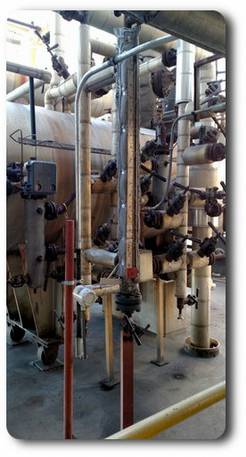
I was given the project to remedy this. I specified and procured two magneto-restrictive level transmitters with shuttle indicators, a PLC, and all associated wiring and hardware. The drip and dump valves were refitted with electro-pneumatic valve positioners and the system was re-commissioned. Additionally, all pressure and temperature signals used to measure heater performance were connected to the new PLC. All level control problems and the continual alarms were eliminated.
Low NOx Burner Upgrade
I was asked to oversee the development and installation of the electrical and the controls portion of this project. I worked with the project manager and the contractors during development, factory acceptance testing, installation, commissioning, and tuning. Additionally, during this outage I engineered and oversaw the replacement of the existing O2 probes with newer models which also measure CO, allowing the unit to be retuned and operate more efficiently.
Natural Gas Booster Skid
The control system for the compressors that boost natural gas pressure for the LM6000 turbine was nearing obsolescence and was also the last PLC of its brand in the plant. A project was created to replace it with a new PLC of a brand that is well supported at the plant and to address some of the control's shortcomings. I served as controls engineer and project manager for this project, including design, procurement, logic development and testing, installation, commissioning and tuning.
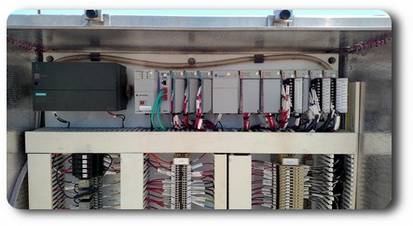
Several improvements were made to the controls. I created a new operational mode with a sliding pressure output that varies with the load demanded by the turbine to save power and wear on the compressors. Also, I authored a cold weather valve test routine to verify that the control valves on the skid were not frozen as they were prone to do during the colder months.
Plant SCADA, Historian, and HMI Systems
My responsibilities included building and maintaining the many SCADA, historian, and HMI systems at Apache. Over the last three years I worked at Apache, I implemented virtualized SCADAs and HMI clients that use thin client for operator consoles. This reduced the number of physical machines by 30% and eliminated substantial overhead from my position. Virtualization also allowed simpler hardware upgrades and robust backups.
Web Portals and Misc Programming
I developed and supported several intranet-facing web servers. These pages access and display historical and live data to support fuel and energy traders, dispatch, operations, and management.
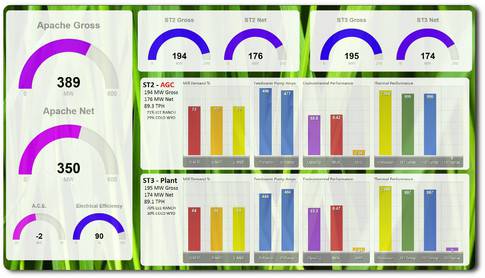
Additionally, I have developed many software applications and scripts that support alarm analysis, system backups, system audits, thin client administration, HMI administration, and other activities.